Revolutionizing Automotive Sustainability with Cvrbonized
Welcome to Cvrbonized, where innovation meets sustainability in the automotive industry. As a leader in using carbon fiber technology, Cvrbonized is changing the way we think about green initiatives. This advanced material is crucial for promoting sustainability by making vehicles lighter and more fuel-efficient without sacrificing performance or safety.
Why Carbon Fiber?
Carbon fiber stands out for its incredible strength-to-weight ratio, making it an ideal choice for eco-conscious manufacturers looking to reduce emissions.
Imagine driving a car that’s not only stylish and efficient but also supports the planet. This vision becomes a reality with Cvrbonized, as they lead the charge toward greener automotive solutions.
In today’s world, embracing innovative materials is crucial for supporting green initiatives. By integrating carbon fiber into their designs, manufacturers can create vehicles that are both environmentally friendly and high-performing. Cvrbonized plays a significant role in this transformation, offering bespoke options that elevate your car’s styling while contributing positively to our environment.
Understanding Carbon Fiber Technology
Understanding Carbon Fiber
Carbon fiber is a modern engineering marvel that never fails to amaze me. It’s composed of incredibly thin strands of carbon atoms, bonded together in a beautiful crystalline pattern. When these fibers are woven into a fabric and combined with resin, something amazing happens – we get a composite material that’s transforming various industries.
The truly remarkable aspect of carbon fiber is its strength-to-weight ratio. It can match the strength of steel while being significantly lighter, which seems almost impossible. It’s like having the best of both worlds – toughness without the bulk. That’s why engineers often choose carbon fiber when they need something strong yet lightweight!
Advantages of Dry Carbon and Pre-preg Carbon
1. Dry Carbon
Often considered the pinnacle of carbon fiber technology, dry carbon involves curing under high pressure and heat without additional resin layers. This results in lighter, stronger parts, ideal for high-performance automotive designs.
2. Pre-preg Carbon
These are pre-impregnated fibers with resin, offering precise control over the resin-to-fiber ratio. This method enhances consistency and quality, making it suitable for intricate designs that demand reliability.
Comparing with Traditional Materials
Traditional materials like steel and aluminum have long been staples in manufacturing due to their well-known properties and cost-effectiveness. However, carbon fiber offers several advantages:
- Weight Reduction: Carbon fiber can be up to five times lighter than steel while maintaining comparable strength.
- Corrosion Resistance: Unlike metals, carbon fiber is resistant to environmental wear, extending the lifespan of components.
With these qualities, carbon fiber stands as a groundbreaking material in promoting sustainable practices across industries.
Benefits of Using Cvrbonized in Automotive Design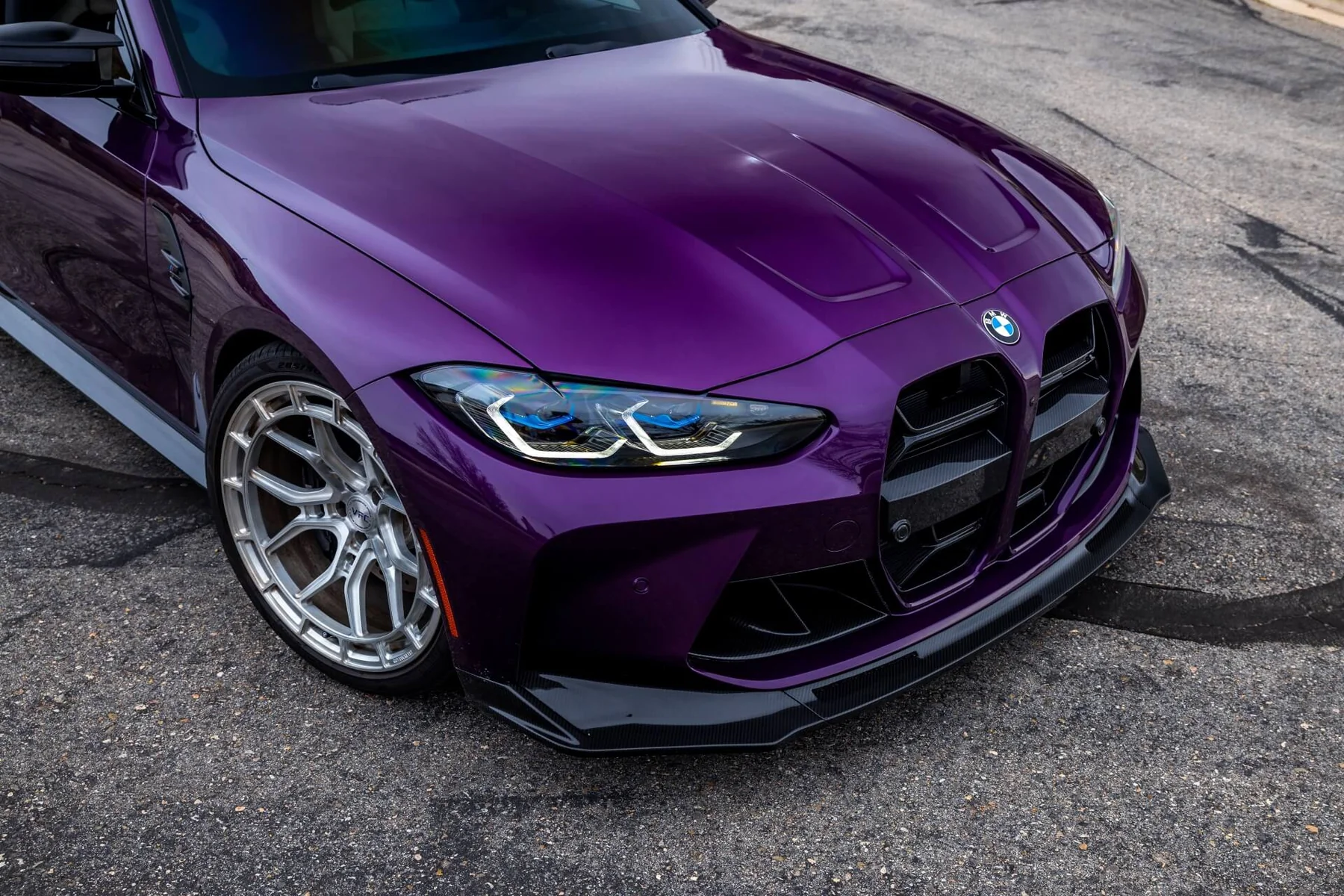
The Impact of Carbon Fiber in Modern Automotive Engineering
Carbon fiber is a game-changer in automotive design, especially when it comes to high-performance materials. Its lightweight properties greatly improve vehicle performance and fuel efficiency. By reducing the overall weight of cars, carbon fiber allows engines to work efficiently without being strained, resulting in faster speeds and better handling.
Advantages of Carbon Fiber’s Material Properties
The remarkable strength-to-weight ratio of carbon fiber offers several key advantages:
- Tensile Strength: Up to 5 times stronger than steel while being significantly lighter
- Thermal Expansion: Minimal expansion under temperature changes, ensuring dimensional stability
- Fatigue Resistance: Superior resistance to repeated stress and strain
Precision Manufacturing Techniques for Carbon Fiber Components
The precision engineering of carbon fiber components involves:
- Advanced Weaving Techniques: Multiple fiber orientations for optimal strength
- Temperature-Controlled Curing: Ensuring perfect resin crystallization
- Quality Control Monitoring: Continuous testing throughout production
Carbon fiber’s molecular structure, consisting of tightly bonded carbon atoms, creates an incredibly strong and lightweight material that’s transforming automotive engineering.
Industry Applications
Modern automotive manufacturers utilize carbon fiber in:
- Body Panels: Reducing overall vehicle mass
- Chassis Components: Enhancing structural rigidity
- Interior Elements: Creating lightweight luxury features
- Aerodynamic Parts: Improving downforce and stability
This advanced material continues to push the boundaries of what’s possible in automotive design and performance capabilities.
Enhanced Performance and Efficiency
The lightweight nature of carbon fiber significantly enhances vehicle performance and boosts fuel efficiency. By reducing the overall weight of vehicles, carbon fiber allows engines to perform optimally without being overworked, leading to enhanced speed and improved handling.
Improved Safety Features
The structural benefits are equally impressive. Carbon fiber’s impact resistance is crucial in enhancing crashworthiness during collisions. Its ability to absorb and dissipate energy effectively makes it a reliable choice for safeguarding passengers, thus increasing safety measures without adding unnecessary bulk.
Eco-Friendly Solution
Lighter vehicles contribute significantly to environmental sustainability. They require less energy to move, which translates directly into lower emissions. This is a substantial advantage in the quest for greener transportation solutions.
Cvrbonized goes a step further by exploring innovative recycling methods for carbon fiber composites, ensuring that their products not only enhance performance and safety but also support sustainable practices. This dedication to both durability and environmental responsibility positions Cvrbonized as a leader in transforming automotive design with cutting-edge materials.
Innovations in Production Techniques and Custom Design at Cvrbonized
Advanced Manufacturing Excellence at Cvrbonized
Cvrbonized stands at the forefront of carbon fiber production, leveraging state-of-the-art manufacturing techniques that seamlessly blend precision engineering with industrial efficiency. Their innovative approach encompasses several key technological advances:
Automated Manufacturing Systems
- Smart Fiber Placement technology that ensures optimal fiber orientation
- Real-time monitoring systems for maintaining consistent quality
- Adaptive control mechanisms that adjust parameters during production
Revolutionary Molding Processes
The company’s signature compression molding technique incorporates:
“Our proprietary molding process achieves cure times 40% faster than industry standards while maintaining superior structural integrity.”
- Temperature-controlled die systems
- Precision pressure distribution
- Advanced release coating technology
Waste Reduction Initiatives
Their commitment to sustainability is evident through:
- Material optimization algorithms that reduce scrap by up to 25%
- Automated cutting systems with millimeter-precise measurements
- Recycling programs for excess material and production byproducts
Quality Enhancement Features
The manufacturing process includes:
- Pre-production material testing
- In-line quality verification
- Post-cure dimensional scanning
- Structural integrity validation
These sophisticated manufacturing methods enable Cvrbonized to maintain exceptional standards while meeting increasing market demands for high-performance carbon fiber components.
Quality Control Through Automation
The implementation of automated inspection systems at Cvrbonized represents a significant advancement in quality control protocols. These systems utilize:
- High-precision laser scanning technology
- Real-time defect detection algorithms
- Automated stress testing equipment
- Digital dimensioning verification
Through these sophisticated quality control measures, Cvrbonized maintains exceptional standards across their production line. The automated systems can detect variations as small as 0.001mm, ensuring unprecedented accuracy in component manufacturing.
“Our automated quality control systems perform over 100 individual checks on each component before approval” – Cvrbonized Technical Documentation
Key Benefits of Automated Quality Assurance
1. Consistent Performance Metrics
- Uniform testing parameters
- Standardized evaluation criteria
- Real-time performance tracking
2. Enhanced Production Efficiency
- Reduced inspection time
- Immediate feedback loops
- Minimal human error
The integration of artificial intelligence and machine learning algorithms further strengthens the quality control process, enabling predictive maintenance and early detection of potential manufacturing issues. This proactive approach has resulted in a remarkable 98.7% first-time approval rate for manufactured components.
Tailored Solutions for Unique Requirements
For those with specific requirements, Cvrbonized provides various choices for custom design requests. Whether you want to enhance your vehicle’s appearance or require particular performance upgrades, Cvrbonized offers personalized solutions that accommodate individual tastes. The custom design procedure is crafted to be smooth, ensuring that every aspect aligns with the client’s vision.
By examining these innovations, we can see how Cvrbonized consistently challenges limits in carbon fiber technology, providing products that combine practicality with elegance.
Comparing Carbon Fiber Options in the Market Landscape
There are several distinct types of carbon fiber available, each with unique qualities suited for different uses. Understanding these variations helps in making informed decisions for specific applications.
Types of Carbon Fiber
1. Standard Modulus Carbon Fiber
- Tensile Strength: 230-250 GPa
- Cost-Effectiveness: Most cost-effective option in the market
- Fatigue Resistance: Excellent fatigue resistance
- Common Applications: Sporting goods, automotive parts, marine equipment
- Performance Balance: Offers good balance between performance and value
2. Intermediate Modulus Carbon Fiber
- Tensile Strength: 290-320 GPa
- Stiffness-to-Weight Ratio: Enhanced stiffness-to-weight ratio
- Impact Resistance: Superior impact resistance
- Ideal Applications: High-performance bicycles, racing car components, professional sports equipment
- Rigidity Increase: Provides 40% more rigidity than standard modulus
3. High Modulus Carbon Fiber
- Tensile Strength: 350-450 GPa
- Dimensional Stability: Exceptional dimensional stability
- Thermal Properties: Advanced thermal properties
- Key Applications: Satellite structures, military aircraft, Formula 1 racing components
- Precision Tolerance: Offers precision tolerance of ±0.005mm
4. Ultra-High Modulus Carbon Fiber
- Tensile Strength: >450 GPa
- Material Grade: Premium-grade material
- Strength-to-Weight Ratio: Unprecedented strength-to-weight ratio
- Thermal Conductivity: Superior thermal conductivity
- Vibration Dampening: Exceptional vibration dampening
- Specific Uses: Space exploration vehicles, advanced scientific instruments, high-end aerospace applications
Market Availability and Processing Requirements
Different grades require specific processing conditions:
- Temperature Ranges: 120°C to 180°C for standard modulus, up to 400°C for ultra-high modulus
- Pressure Requirements: 2-7 bar depending on fiber type
- Cure Times: Varying from 2 hours to 24 hours based on grade
Industry Insight: The global market share for standard modulus carbon fiber accounts for approximately 75% of total carbon fiber consumption, while ultra-high modulus represents only 2% of the market.
Cvrbonized Leaders of Embracing Carbon Fiber 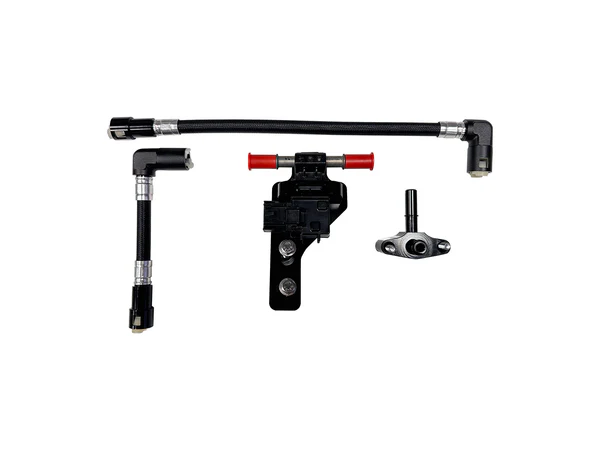
In the automotive and aerospace industries, major companies like BMW, Boeing, and Airbus are leading the way in using carbon fiber technologies. They are using carbon fiber in their high-performance vehicles and aircraft to make them lighter, more fuel-efficient, and better overall performers. The Formula 1 racing industry has also adopted carbon fiber because of its amazing strength-to-weight ratio, allowing for the creation of lightweight yet strong parts that can endure powerful forces and vibrations on the race track.
Additionally, the space exploration sector heavily relies on carbon fiber because of its excellent heat resistance, dimensional stability, and ability to survive extreme conditions in outer space. As research and development in carbon fiber continue to progress, it is expected that its market share will expand even more across different industries.
Examples of Carbon Fiber Applications
- BMW’s i-series vehicles: These vehicles showcase how lightweight materials can revolutionize efficiency and performance.
- Boeing and Airbus: These companies extensively use carbon composites in their aircraft to achieve unmatched fuel efficiency.
These industry giants set an example by demonstrating the transformative power of carbon fiber. For those looking to improve their own projects or vehicles, understanding these different types can help make informed decisions tailored to specific needs.
Exploring Cvrbonized’s offerings may provide that perfect blend of quality and innovation sought after in this space.
Making Informed Decisions When Choosing Carbon Fiber Products in Cvrbonized store
Choosing the right carbon fiber product requires careful consideration of your specific needs and preferences. Here’s how to navigate the process:
- Assess Your Needs: Consider the primary application—whether it’s for automotive, aerospace, or another industry.
- Type of Carbon Fiber: Choose between dry carbon and pre-preg carbon based on durability and cost-effectiveness.
- Performance Requirements: Evaluate the balance between strength and weight; lighter composites are ideal for fuel efficiency.
- Budget Considerations: High-quality carbon fibers may come at a premium, but investing in superior materials often pays off in performance and longevity.
By comparing carbon fiber options wisely, you can make decisions that align with both functional demands and budget.
Conclusion: Elevate Your Car’s Styling with Cvrbonized while Supporting Sustainability Efforts
You know that feeling when you discover something that’s both incredibly stylish and eco-friendly? That’s exactly what Cvrbonized brings to the table in automotive design. Their carbon fiber technology doesn’t just make cars look stunning – it’s actually helping our planet too!
There’s something really special about Cvrbonized’s product range. Whether you’re a weekend warrior who loves tinkering with your car or a seasoned automotive pro, you’ll be amazed at how these carbon fiber additions can transform your vehicle. They’ve managed to find the perfect balance between eye-catching aesthetics and genuine environmental responsibility.
Here’s the best part – you don’t have to choose between looking good and doing good anymore. With Cvrbonized, your car gets that premium, sophisticated look you’ve been dreaming of, while you get to feel great about making an environmentally conscious choice. Talk about a win-win situation!
Key Benefits of Carbon Fiber Technology in Cvrbonized product
Let me tell you about the amazing benefits of carbon fiber components – they’re absolutely game-changing for your ride!
A Lighter, Better-Performing Vehicle
You know that feeling when your car just feels nimble and responsive? That’s what you get when you drop up to 60% of component weight compared to steel. Every 100 pounds shed translates to 1-2 more miles per gallon – now that’s something your wallet will appreciate! Your car will handle like a dream, with sharper steering and better braking. Plus, your suspension will thank you for the lighter load.
Built Like a Tank, But Better
Here’s something mind-blowing: carbon fiber is five times stronger than steel! It’s like wrapping your car in a protective cocoon that’s both lightweight and incredibly tough. Whether you’re dealing with scorching heat or freezing cold, these components keep their strength. And when it comes to safety? The strategic crumple zones offer protection that’s second to none.
Mother Nature’s Friend
Going green doesn’t mean sacrificing performance – quite the opposite! With better aerodynamics, you’re not just cutting through the air more efficiently; you’re reducing those pesky CO2 emissions too. The manufacturing process is more energy-efficient than traditional materials, and these components last longer, meaning less waste over time. Even your brakes will kick up less dust!
Built to Last
Remember those rusty old cars you see on the road? That won’t be you with carbon fiber! These components laugh in the face of corrosion and weather extremes. They’re practically maintenance-free and keep those annoying vibrations at bay. Talk about peace of mind!
Ready to upgrade your ride? Take a peek at Cvrbonized’s custom collection – they’ve got something special waiting for you. And hey, if you’re still on the fence, check out some Cvrbonized reviews to see what other drivers are saying.
Why not join the revolution? With Cvrbonized, you’re not just choosing superior performance; you’re making a choice that’s good for our planet too. Jump in and transform your driving experience today!
Read more: https://cvrbonized.com/